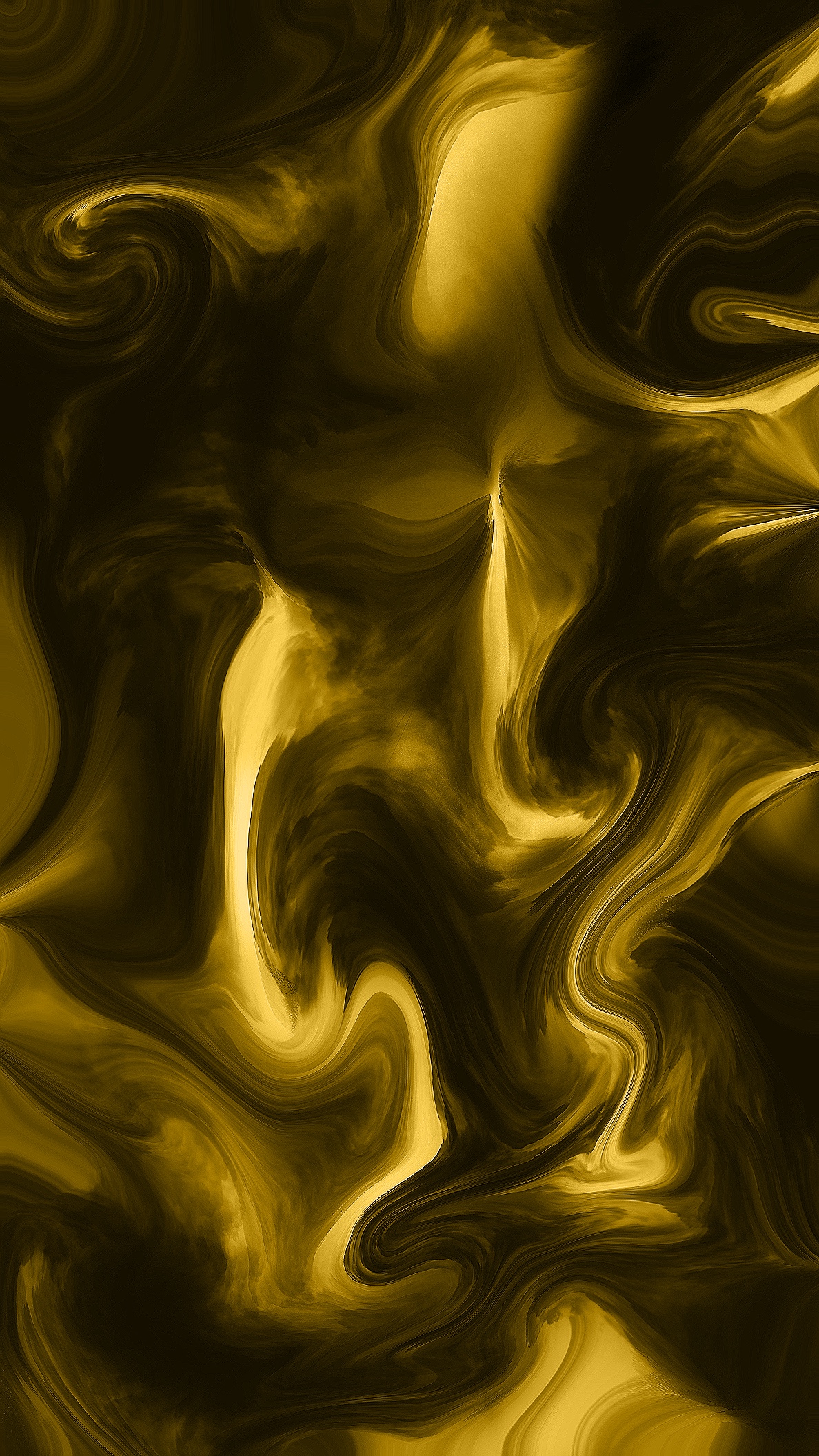
Costs of Production
Stages of Production:
Primary:
This involves acquiring raw materials. For example, metals and coal have to be mined, oil drilled from the ground, rubber tapped from trees, foodstuffs farmed and fish trawled. This is sometimes known as extractive production.
Secondary:
This is the manufacturing and assembly process. It involves converting raw materials into components, for example, making plastics from oil. It also involves assembling the product, e.g. building houses, bridges, and roads.
Tertiary:
This refers to the commercial services that support the production and distribution process, eg insurance, transport, advertising, warehousing, and other services such as teaching and health care.
Aims of Firms:
Firms exist to produce goods and services and to gain maximized profits, and they may be in the private or public sector.
Private Sector:
Those owned and operated by private enterprises.
Public Sector:
Those owned and operated by the government.
Profits:
Firms have different aims, however, the primary aim of every firm is to make profits.
Profit is the difference between the revenue earned from the sale of products minus the cost of production,
Profit = Total revenue – total cost
Why are Profits Important?
It is the primary aim of every business. It is a reward for the risk-taking ability of an enterprise. It is needed for the long term survival of a business. Profits need to be reinvested for the expansion and growth of the business.
However, profit maximization may be difficult to achieve as increasing the prices for the consumers will result in lower demand and sales of the products. Hence, firms will aim to earn a satisfactory level of profits – this is called satisficing.
Other Aims Include:
Increase in market share:
Market share is the percentage of sales held by a business or brand. The firm/brand with a higher market share becomes the brand leader.
Social Aims:
Some businesses aim to serve society such as people in need, animal welfare, protecting the environment.
Productivity:
Productivity measures the amount of output that can be produced from a given amount of input (factors of production).
A firm becomes more efficient when productivity increases.
Productivity = increase if more output or revenue is produced from the same amount of resources.
Productivity is measured by divided total output/total input.
However, firms are more interested in labor productivity calculated through total output/number of workers.
Workers and their efficiency are very important to a firm as wages form the largest proportion of rims cost of production. Some problems with calculating labor productivity are – some output is not quantifiable such as services, teachers, soldiers, waiters, police, and researchers. Another problem is that it does not take into account the quality of work.
Firms can Increase Labor Productivity by:
- Training workers to improve their skills
- Rewarding increasing productivity with performance-related pay.
- Providing better machinery and tools.
- Increasing job satisfaction by improving the work environment, promotion prospects, involved workers in the decision-making process.
If productivity increases, output per labor increases, and the average cost of producing each unit decreases, and profits will tend to increase.
Lower costs can be passed on to consumers in the form of lower prices to increase consumer demand and sales.
As sales increase, the firms will expand and enjoy the benefits of being a large firm – more profits, brand values, status, and prestige.
Division of Labour:
Division of labor is when the production process is divided into smaller tasks and each worker concentrates on one part of the job.
Division of labor leads to specialization. Specialization can be job-wise, country wise or firm-wise.
(e.g. Ms. Susan is an economics teacher whereas in primary school you had one teacher teaching you all the subjects)
Advantages:
- More goods and services can be produced.
- Full use is made of employees abilities
- Time is saved
- It allows the use of machinery
Disadvantages:
- Work may become boring.
- Workers may feel alienated.
- Products become too standardized
Fixed Costs:
Costs that do not vary with the level of output. They have to be paid even before productions/operations.
Examples:
- License
- Insurance
- Loan Repayment
- Capital
- Machinery
- Rent
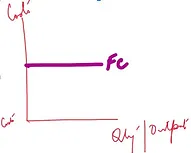
Variable Costs:
These are costs that vary depending on the level of output. They increase with the level of output.
Examples:
- Raw Materials
- Wages
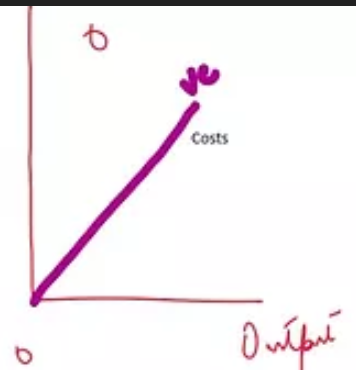
Total Costs:
The Total Cost can be calculated by attaining the sum of the fixed costs (FC) and the variable costs (VC)
TC= FC + VC
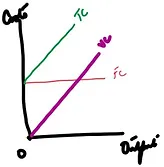
Revenue:
Revenue, simply put, is the income from the sale of goods. This can be calculated by multiplying the price by the quantity sold
revenue = price x quantity sold
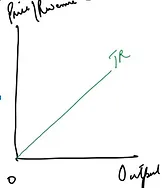
Profit:
Profit = total revenue > total cost
Loss:
Loss = total cost > total revenue
Break-Even Point of Production:
total cost = total revenue
